|
To achieve operational excellence in retail inventory management, there are three key objectives to address: Supply management, presentation stock and poverty distribution. These three points will help you take your retail business to the next level and optimize inventory by taking the best supply chain advice. Supply Management in Retail To begin supply management in the retail sector, it is necessary to define which items are part of the supply and which products should be discontinued. For this, a tool that can help us is the stocking index matrix, which allows the user to classify the products according to certain criteria to be met, for example, daily sales, margin or profitability. These criteria are then assigned a score that sums to 100 to achieve a baseline and threshold. Additionally, this matrix must include an evaluation period , six months or one year, depending on the type of business. Finally, the sum is carried out and the cut-off criteria are obtained: From 50 to 100, the product must remain active in the store.
From 30 to 49, additional analysis is required, for example: can work be made to order or direct delivery from supplier to customer? and From 0 to 29, products are candidates for discontinuation. This matrix should always be considered as a parameter and a guide, but it must be reviewed by the teams to make decisions . It all depends on the business of each industry and sector, therefore, each item can behave completely Japan Telegram Number Data differently depending on the business. Product life cycle Once the products are classified according to the stocking index, they can be classified again according to their stage in the life cycle. Introduction stage, the first purchases and first replacements are made , with an initial forecast and considering the filling in branches. Then follows the growth stage, where the product begins to be sized in a better way, begins to gain a sales rhythm and begins to become known to the public. It is essential to generate alerts for optimal replacement and avoid stockouts or overstocks. The third stage is maturity, this is where it starts to function regularly.
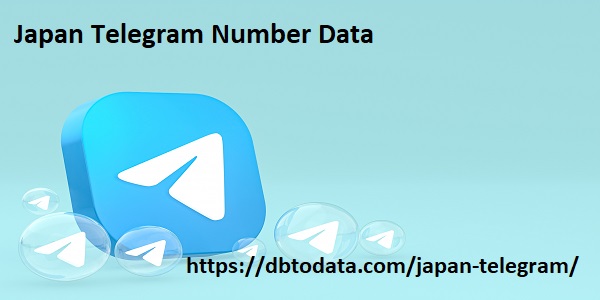
Replenishments are automatic, managed by KPIs and with a known operation. However, you have to be careful when the item reaches decline, the fourth and final stage of the product life cycle. The product begins to decline in sales and does not have the same performance as before, at this stage it is essential to be attentive and make key decisions: is the product discontinued? What happens to the remaining stock? is it redistributed? Is it liquid? Is it returned to the supplier? These are questions that must be resolved at this point. How to build an ABC Once the supply is defined, with a stocking index matrix and knowing what stage of the life cycle they are in, we can build an ABC analysis. This ABC ranking mainly serves to prioritize articles based on certain criteria. To build an ABC, one or more criteria must be selected , it can be sales, order lines, units sold, or the criteria that the business requires. Then the weight of each SKU is defined with respect to the total sample and then ordered from highest to lowest and finally segmented based on the accumulated weight.
|
|